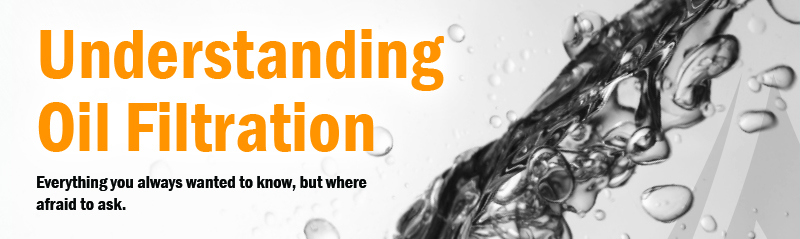
Contamination: The Problem
Contamination control is an important part of a proactive maintenance strategy. The first step in keeping lubricants clean, cool and dry is to address the existing contaminants and measure their potential impact on the machinery and oils (failure modes). With this information, it will be easy to take the appropriate actions to maintain lubricants in good condition.
As surprising as it may seem, most oil purchased today has not been filtered before being sold. Yes, it is newly refined and looks translucent, but it has many more particles then would be expected from new oil. Typically, new oil being delivered to customers are class 22/18/16 and sometimes worse. This puts the end user in the position of having to filter the oil before putting it into service to assure it will not cause premature wear on the machinery.
As soon as this oil is put into service, there are two primary types of contamination that your equipment is exposed to…DIRT and WATER.
Particulate or dirt contamination, once inside your equipment, will continue to generate new particles.
These particles act as a catalyst for oxidation and additive depletion, further degrading the condition of the oil. Equipment exposed to a humid or moisture rich environment can see severe lubricant degradation caused by water. Water can cause oxidation within the lubricant and corrosion inside the equipment.
All these factors threaten equipment reliability and lubricant quality; however, they can be effectively controlled with some simple, yet effective, preventative maintenance techniques. The simple and easiest way to keep contaminants out is to avoid practices that risk exposing lubricants to these contaminants.
Achieving Clean Oil
Set Oil Cleanliness Targets The ISO Code refers to a logarithmic scale used in determining the cleanliness of lubricating fluids. It is known as ISO 4406:1999. The number of particles in 1 mL of fluid are counted and arranged according to size. The three-code system assigns a number to particles equal to or greater than 4 micron, 6 micron and 14 micron. This allows for a simple yet effective means to quantify and monitor fluid cleanliness. This standard serves as a guideline only and should be viewed as a ceiling level. The ISO Code target should also take into consideration the severity and cost of failures as well as the reliability goals of the organization. Therefore, setting a lower ISO Code and moisture targets will translate into greater reliability and life extension. Therefore, as the expression goes, keep the oil “cool, clean and dry.” This leads us to the second step, which involves the implementation of activities to achieve the goals set forth above.
Take Action to Reach Targets Achieving any type of goal requires that we take action. In this context it requires that two specific actions be taken. First, reduce contaminant ingression. In other words, keep particles from getting into the gearbox. Follow good housekeeping procedures in the storage, handling and dispensing of lubricants. Ensure that lubricants are kept clean and dry. Avoid cross contamination by clearly labeling containers as to the oil type. Use filter carts to clean and dispense oil from drums. Portable containers can be directly filled from the filter cart, ensuring clean oil is added to the gearbox. During maintenance events, take great care to minimize the entry of contaminants into the gearbox. Add oil from a portable filter system with quick disconnect fittings. Breathers should have a filter and desiccant to remove ambient dirt, dust and moisture. Use labyrinth seals and V-rings. Second, improve filtration. Remove particles and water quickly. A well-designed filtration system will effectively remove not only solid particles, but also moisture and soft contaminants. A well-designed contamination control system incorporating in-line and offline filters will reach oil cleanliness targets and provide operational economy. A common myth is that increased filtration costs outweigh the benefits of achieving cleaner oil. Savings usually outweigh costs by great margins because of longer filter service life, lower oil consumption, and extended gearbox and bearing lifetime.
Monitor Oil Cleanliness The final element of an effective contamination control program is to regularly monitor the oil’s condition and take appropriate action when goals are not met. Oil monitoring can be accomplished in the field or by an experienced laboratory. Monitoring indicates how well the filter system is performing and also alerts the user to potential failures. A typical test slate will include the ISO Code, water content, acid number, elemental analysis and viscosity. Oil sampling procedures should be carried out by trained personnel to ensure representative samples. Samples should be drawn from live zones and preferably during operation. As mentioned earlier, an offline filter with an integrated sample valve provides adequate circulation for sampling, even when the turbine is shut down. Sampling frequency should be carried out every six to 12 months. The future of condition monitoring will include the use of online sensors to provide real-time data.
In summary, the three steps to an effective contamination control program are:
- Define targets for particle and water contamination and oil properties
- Instigate remedial action as necessary to reach targets
- Monitor contamination levels against target levels and maintain safe levels.
Types of Systems
Hydraulic Systems: With hydraulic systems, fluid is used to transmit power of components, such as motors and rams. The fluid passes through the valves which direct the oil to the working components the higher the system pressure, the closer the tolerances that the components will need to maintain. As the ram is extended and retracted a small amount of contamination is brought into the system. To the naked eye the ram looks smooth but if viewed under a microscope it has many peaks and valleys.
There can also be airborne contamination that can drop onto the cylinder and be drawn into the oil past the seal. This small particulate material is suspended in the oil until removed by the filter or drained at the next servicing. AS the small contamination (silting) build up, it can bind or stick valves. Servo valves are particularly sensitive to silting. Vane pumps and piston pumps are both components that have an elevated degree of sensitivity to contamination. A 3-5 micron clearance of the vane tip to the housing puts particles under pressure, eroding the metal like a sand blaster.
Gear Systems: Gear oil provide lubrication which allows gear teeth to slide past each other. The fluid also keeps the sliding surfaces cool. Contamination in the oil will cause abrasive wear on the teeth surfaces, generating more particles. Oxidation (thickening) of the oil due to elevated temperatures in the presence of oxygen is an issue that must be controlled to keep gear oils serviceable. Condensation or moisture in the oil, even in small amounts, acts as a catalyst in oxidation and the formation of acids in the oil.
Transmissions: The function of this fluid is threefold: gear lubricant, hydraulic fluid in the torque converter, and a coolant. While each function is best performed as a clean fluid, the clutch packs in the system contribute wear particles continually. If this contaminate is allowed to build up in the fluid, it will wear on the gears, erode the vanes of the torque converter, and accelerate the wear on the clutch packs.
Engines: Engine oil provides lubrication to all sliding parts of the engine; sealing between the ring and the cylinder wall, cooling the pistons, and keeping the components clean. This is a demanding service for the engine oil. The 2-3 micron gap between the ring and the cylinder wall provides a seal to keep combustion gases from the crankcase. As the contamination builds up, particles will wedge between the two surfaces and break the oil seal allowing combustion product blow-by and increasing oil usage. This will also increase the wear to the surfaces due to abrasive bridging. The contamination bridge also creates wear on the bearing surfaces, camshaft, and gears.
Diesel Fuel: The combination of high pressures, reduced lubrication, and contamination is forcing companies to realize the need for contamination control. Additionally, water in the fuel will promote algae growth in the tanks and if allowed to be pumped into the injector can cause catastrophic failure. Similar to hydraulic systems, the need for contamination control is the fuel system is just as critical. Cleaner fuel reduces wear on expensive and sensitive fuel injector parts maintaining peak performance and delivering better fuel economy. If also reduces filter plugging, improves fuel system longevity, and decreases downtime.
Basic Forms of Oil Filtration
There are two basic forms of oil filtration: in-line or permanent and kidney loop or off-line. Most circulating systems have in-line filters on the pressurized supply line. This is so oil that is fed to the moving components is clean and dry. However, most in-line filters cannot adequately control contaminants without significant and costly upgrades. When this is the case, kidney loop filtration is an excellent, cost effective solution.
Off-line filtration, sometimes called kidney loop filtration, is designed to filter a small stream of fluid; returning the filtered oil to the sump of the system. Portable systems (Figure 1) allow for quick and efficient filtration without affecting the normal functions of the system. They generally can be used for multiple systems. Permanent or in-line filtration (Figure 2) generally provides more efficient contamination control because it generally operates 24/7. However, these types of systems are not portable, as they are generally affixed permanently to the equipment.
There are a number of configurations and variations for filtration systems…
Full Flow: Designed to filter fast, full flow filters protect downstream components from larger sized particulate matter. These systems typically use surface type filters (spin-ons). These work by direct interceptions of particle larger that the pore size of the media. Dirt is trapped on the upside of the media with the holding capacity limited by the number of pores in the media. The dirt holding and water holding capacity is often measured in grams.
Depth Type: Designed to filter slowly, depth filters protect downstream components from the smaller sized particulate matter. These systems use a tightly wound cellulose media. These filters work by both direct interception and absorption (molecular attraction of particles). These filters use several types of media to achieve the goal of holding particles. The fluid must take a longer path through the filter before exiting. Normally these have larger dirt and water holding capacitates that is measures in pounds.
Contamination Control Program
Contamination control is an essential part of an effective maintenance program. It provides what is perhaps the single greatest opportunity for gains in terms of reliability and life extension. Significant savings are achieved through longer oil and component lifetime.
The benefits of improving oil cleanliness will mean the following:
- increased equipment lifetime
- longer oil service life
- reduced lubricant consumption
- decreased environmental impact
The relationship between lubrication quality and maintenance costs is inversely proportional. Financial gains are made when the oil quality and cleanliness levels are improved. Understanding the different contaminant types and where they come from will help owners and operators to design an effective program. Such a program sets cleanliness targets, takes specific steps to restrict the ingression of contaminants, and removes them efficiently by upgrading filters to prevent the accumulation of particles, wear and oxidation byproducts. Finally, the program is brought into balance by monitoring the progress and taking appropriate action to again reach the target cleanliness. Given the damage contamination can bring to equipment, controlling it is well worth the effort.
In summary, the three steps to an effective contamination control program are:
- Define targets for particle and water contamination and oil properties
- Instigate remedial action as necessary to reach targets
- Monitor contamination levels against target levels and maintain safe level
Download Understanding Oil Filtration PDF