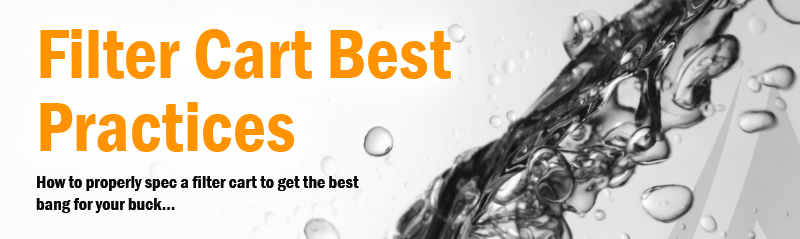
The Evolution
As times and practices have changed over the years, the use of a filter cart has gone from being something that was just used on critical equipment to something that is a staple in every engineer’s lube room. While industry practices have changed and more and more organizations have placed a greater emphasis on equipment reliability and better lubrication practices, they have also come to realize just how valuable a filter cart can be in helping achieve these best practice goals. However, it has become apparent that a lack of knowledge regarding how to select the right filter cart, from both the customer and the distributor, can cause several mistakes that prove costly. The following are some things to take into consideration in order to help eliminate costly mistakes and obtaining maximum value for your investment.
Intended Use
The filter cart isn’t just for offline filtration anymore, now, more than ever, it’s being used for dispensing new oil, performing routine oil changes and flushing new components. Before selecting your filter cart, you should consider things like size and weight. Ideally, your filter cart should be able to easily reach each system you’re trying to clean up. If the size and weight of the cart makes it too cumbersome to use or if it is difficult for operators to get it to the desired location, you might want to consider alternative options.
Power Source
Many of the carts available out there are offered with various power sources. Most suppliers offer 110/220V, Single and Three Phase motors, as well as various air motor options. So make sure that you speak with your supplier to make sure the power source you need or have available in your plant is available.
Flow Rate
This is usually the most complex of all your selections because there is no “one size fits all” when it comes to selection of the appropriate pump to use. Before making a selection, you should consider all the various applications you plan to use your cart for, such as fluid viscosity, oil temperature, time and fluid compatibility. Not all pumps are equal and there should be careful thought put into this decision. A pump designed for ISO 32 hydraulic oil will not work or perform acceptably for an ISO 680 gear oil. The maximum pump flow rate should be at least 10 percent of the total pump volume. A 10- gallon reservoir requires no more than one GPM for completed fluid turnover. Insufficient flow will result in long turnover time. At a minimum, the pump you select should have the capability of turning over the entire pump capacity at least one time per hour.
Filter Type
Before you choose a specific filter element, you must first determine the desired ISO cleanliness code you’d like to achieve. You should always select filters that have a micron rating that is at least as small as the particle size with which you are interested in filtering. Most quality filter carts will utilize dual elements that run in series; either a water removal element or larger micron element is often used as the first filter. A finer micron filter element, or polishing element, is then used as the second in the series. This is done in order to help extend the life of the smaller micron element and maximize filter efficiency. Another thing to consider is the beta rating of the elements that you select. The higher the beta rating, the more efficient the filter element will be. You should always make sure that the element chosen is at lease Beta 200 or higher.
Additional Considerations
When comparing different filter carts, don’t always assume that they are the same. Different manufacturers offer stripped down versions of their carts or use inferior products in order to manufacture low cost options. So, when comparing different carts, make sure you take some of the following things into consideration during your search for the perfect filter cart...
- Color – Find a manufacture that is flexible on color options. Many suppliers offer multiple color options at no additional charge.
- Hoses – Should be, at minimum, steel reinforced, clear PVC; other options include standard hydraulic hose. Standard hose lengths may vary.
- Hose End Configurations – Best practices suggest that you should use some sort of closed fitting, such as an ISO B or Flush Face connector. Other options like wands, although not recommended, are available as well.
- Filter Heads – Should have either slidebar or pop-up indicators to easily identify plugged filters.
- Sample Ports – Can easily be added to any style filter cart and assist in helping to collect oil samples. They are normally installed before and after the filters.
- Tires – Many different styles are available…hard rubber, oil-resistant and flat free. They should be large enough to easily traverse any environment.
- Manual Filter Bypass – While not normally needed, the bypass valve allows you to manually bypass the filter elements if you plan on using your filter carts to evacuate waste oil from various systems.
Other options such as high pressure shutdowns, differential pressure gauges, inlet strainers or filters and particle counters should be evaluated and taken into consideration as well.
Planning & Research
A little planning and research can go a long way in selecting the right filter cart for your needs. Careful evaluation of your situation, in conjunction with your suppliers input, will help you determine which filter cart will best suit your needs. Most suppliers will be able to design the filter carts to meet your exact needs, giving you the most for your investment.
Download PDF of Filter Cart Best Practices White Paper