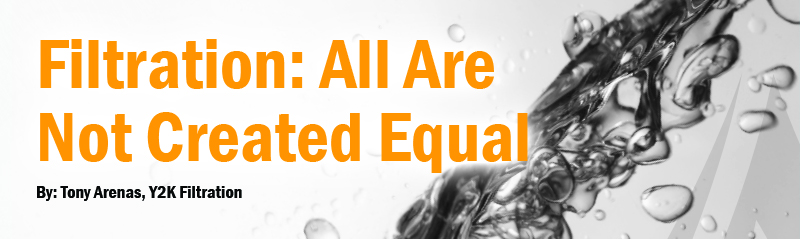
Technological Advancements in Filtration
Although filtration has been around for a long time we have only begun to put focus on understanding the true effects of water and particulate contamination in Hydraulic and Lubricating oil systems. In a world where we have great technological advancements, access to large amounts of data and various ways to collect and analyze it, we have, now, at our finger tips what was once very hard manual work to achieve this data; and it’s this data that creates a true pathway to reliability and a full understanding of the effects this has on these systems. Many people used their experience, intuition and personal connection to the equipment to understand what is needed to keep the equipment running at its maximum potential. In today’s terms we can now begin to remove some of the mystery behind equipment reliability and understand how wear particles and chemistry changing water molecules truly effect the system and its ability to run at extended intervals.
"Call it Good" No Longer Acceptable
The old thinking is let’s dump the oil and change the on-board filter and “call it good” but the reality of this thinking is that this is no longer acceptable in today’s focus on efficiency in addition to reliability and cost effectiveness. More and more reliability and maintenance people have to focus their efforts on utilizing the resources they have in reclaiming used or contaminated oil with shrinking budgets and higher demand for performance. Which is why it is more important than ever to allocate those funds to a filtration system that is going to get you there with the least resistance and up-keep. It doesn’t do any good if you’re spending more time trying to get your filtration equipment to work than using it, or, worse yet, not using it because it is hard to use and the value is not immediately understood. In this case you have spent a sum of money that’s never going to give you the ROI needed to justify additional purchases and show the working metrics of return by using the systems (Payback). The old saying “you get what you pay for” is never the truer than realizing it after the fact, which is why Y2K Filtration manufactures a complete line of standard and custom filtration products, backs it with the industry’s top rated warranty, as well as 100% support of our products; that means if we design a custom or standard filtration system with all information properly provided about the application, we guarantee the highest level of performance and return on investment.
Spend More Upfront to Save In the Future
When it comes to the cost of filtration equipment there’s not a lot of value in attaining a lower cost ineffective system that is easily justifiable from an Operations and Maintenance budget standpoint, but does not provide the level of ROI or system reliability most often times required to maintain the system properly. So you end up spending more money in addition to the initial cost to “make it work” for your system. The alternative is buying the right system up front at a little higher costs that returns in most cases at a higher rate of return than much less efficient systems and accomplishes in much less time. So buyer beware that all Filtration systems are not created equal. If you haven’t read our white paper
“Filter Cart Best Practices” and
“Water and Particulate Contamination in Hydraulic and Lubricating Systems,” I highly recommend these two it gives some great insight in to different systems available and important tips to keep in mind when purchasing your next filtration system.
Taking a Look Closer
One of the main reason for failure in reliability and interval filtration programs is not properly understanding the influencable aspects of the equipment or machine, in addition to improperly applied or undersized filtration equipment. A large sum of money is spent on equipment repairs and maintenance in relation to contaminated systems. The majority of Filtration Equipment manufacturers are trying to capture most applications with just a handful of standard products because the cost to produce those products in bulk makes it more profitable from a production standpoint than a one off system designed specifically for an application, where the cost to produce standard products are spread out amongst a larger quantity; and so this leads consumers having to deal with systems that are either undersized, oversized, not properly applied or lack the efficiency required to keep up with the ingression rates of the machine or equipment. In regards to Filtration systems we too often hear “that’s too expensive, we can’t afford that.” Typically we like to challenge this question in more depth, and ask the reverse, “How can you afford not to?” When it comes to equipment or machines, it is a reality that more money is lost through warranty, re-work and/or replacement parts, than if there was an effective implementation of a good Hydraulic and Lubricant oil filtration program. It really brings light to the saying “Pay me now or pay me later.” So it takes a little adjustment in the way we think to focus on eliminating festering contamination before it has the chance to cause irreversible damage in your system. Fact is that the cost to remove contamination is at a much higher cost than to prevent and maintain it upfront.
So what is the true cost in the scenario? Well it really breaks down to the cost of equipment when it is down for maintenance, or, worst, an unexpected breakdown. What is that cost to the company and your customers? It’s more than the equipment that’s on the line, it’s the customer’s experience, end product, quality and the overall costs to produce that’s really at stake here (Is your customer willing to pay extra for a better product or extra because of production inefficiencies?). One thing is certain, contamination in many forms will always be present, it all comes down to what you do about it and the ability to measure whether or not those practices worked as intended.
Choosing the BEST Filtration System Tips
When choosing the best Filtration system for your application here are some basic required information that would be concerning, if you were not asked when requesting a filtration system. Choosing the correct system is not the outcome of guessing which one might work, or fitting it into a standard set of products offered. It is a calculated process of identifying, understanding and measuring successful results.
- What is the Application?
Example: Hydraulic Press, Paper Machine, Haul Truck, Process Equipment, Etc.
- What is the Operating Temperature Range of the Equipment Going to be When Filtering?
Example: Offline Equipment: 40 Deg. F to 90 Deg. F., Online Equipment: 120 Deg. F to 135 Deg F., Etc.
- What is the Sump or Reservoir Volume in Gallons/Liters?
Example: 10 Gallons, 50 Gallons, 10,000 Gallons, Etc.
- Desired ISO Cleanliness Code?
Example: 16/14/11 Sometimes this can be tough. If application data is provided, this can easily be recommended by the manufacturer.
- What is the Oil Type/Brand?
Different oils have different compatibilities as well as materials compatibility requirements such as Viton Seals vs. Buna. There are different grades of oils and lubricants such as synthetics, gear, fire resistive, etc.
In addition some things to be aware in relation to cost, longevity of the equipment and performance. Where the biggest differences in cost come into play are filtration systems that are attractive in price but lack results, efficiency or durability of premium priced, high efficiency filtration systems.
Y2K Takes the Guess Work Out of the Process
We at Y2K like to take the guess work out of the process by innovative products, diverse application experience and complete application/engineering support. There’s only one right way to have an effectively managed filtration program, and our focus is to educate everyone about the environmental impact of reclaiming oil, the cost savings and the importance of properly applying the correct level of filtration to eliminate waste and costly breakdowns.
As always I recommend contacting Y2K for additional resources and information on your most challenging applications. Take the struggle out of determining if you’re applying the correct level of filtration, and put it on us, so you can focus your valuable time and attention on other important aspects of your day to day job. Most importantly, ask questions and use common sense practices in all your thought process. If your gut is telling you something else, it may be time to listen, because true contamination control and best practices will always make sense in every aspect.
For More Information
Y2K Filtration 3620 N. Lewis Ave. Sioux Falls, SD 57104 | 888-925-8882 |
sales@y2kfiltration.comDownload PDF of Filtration: All Are Not Created Equal